Industrial decarbonization is the process of significantly reducing or eliminating carbon dioxide and other greenhouse gas emissions from industrial activities.
This is crucial for mitigating climate change, as the industrial sector currently accounts for nearly one-third of global carbon emissions as per the World Economic Forum. Key industries like steel, cement, and chemicals are major contributors to these emissions, necessitating a transition to cleaner production methods.
Each industry requires tailored approaches to achieve significant emission reductions and support a sustainable future.
Types of Emissions from Heavy Industry
Industrial decarbonization encompasses efforts to reduce greenhouse gas (GHG) emissions across three scopes, as depicted below:

Source: Environment Energy Leader
Different Methods for Decarbonization

Source: WRI
Industrial decarbonization involves a range of methods to significantly reduce greenhouse gas (GHG) emissions from industrial processes. These methods include:
- Switching to Low-Carbon Fuel/Energy Supply like Clean Hydrogen and Non-Fossil Fuels: This approach involves using alternative low-carbon fuels such as hydrogen (including green, blue, and biohydrogen), biomass (both waste and virgin biomass, and biomass fuels), or low-carbon electricity. These alternatives help reduce the carbon footprint of industrial energy consumption.
- Carbon Capture, Use, and Sequestration (CCUS): CCUS technology captures CO2 emissions from industrial processes and combustion. The captured emissions are then stored underground or utilized in other processes, preventing them from entering the atmosphere and contributing to global warming. You can read more about carbon capture and storage in our previous newsletter.
- Alternative Low-Carbon Novel Processes: Certain industrial commodities can be produced using alternative and innovative production methods that save emissions. Examples include secondary aluminum production and microwave drying in paper production. These novel processes often involve fuel switching to further reduce emissions.
- Facility Retirement/Retrofits: Retiring outdated facilities and retrofitting existing ones with advanced low-carbon technologies can significantly reduce emissions.
- Material and Energy Efficiency: Material and Energy Efficiency aims to reduce emissions by using fewer raw materials, such as through recycling, or by enabling the use of emissions-free materials. They also focus on reducing energy consumption in the production process.
- Electrification with Renewables: Replacing fossil fuel-based energy sources with renewable electricity can drastically cut emissions. This includes electrifying processes that traditionally rely on fossil fuels.
- Material Efficiency and Circularity: Implementing practices that promote material efficiency and circularity, such as recycling and reusing materials, reduces the need for raw materials and minimizes waste.
Key Solutions for each industry:
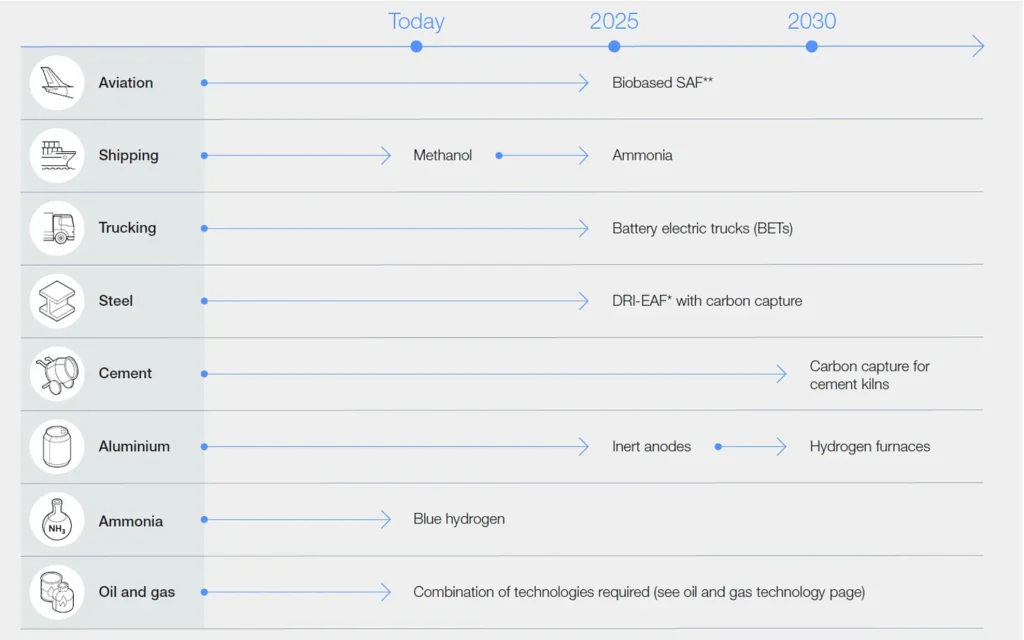
Source: WEForum
We will be covering solutions for the steel, cement, aluminium and ammonia industries below as solutions for transport and energy emissions are covered in our earlier newsletters.
Steel Industry
Key Emissions Sources:
- Energy-related Emissions: Primarily from coal used in blast furnace-basic oxygen furnace (BF-BOF) and electric arc furnace (EAF) processes.
- Process-related Emissions: From the use of coke or natural gas as a reducing agent to convert iron ore into iron.
Key Solutions:
- Direct Reduced Iron-Electric Arc Furnace (DRI-EAF) with Carbon Capture: Uses direct reduced iron as feedstock in electric arc furnaces powered by clean electricity, reducing emissions by avoiding the high carbon footprint of coke.
- Carbon Capture: Captures CO2 emissions from steel production processes and stores or utilizes them to prevent atmospheric release.
Cement Industry
Key Emissions Sources:
- Energy-related Emissions: From fossil fuels used for kiln heating, material grinding, and machinery operations.
- Process Emissions: From chemical reactions during the conversion of raw materials to clinker, notably through limestone calcination.
Key Solutions:
- Carbon Capture for Cement Kilns: Captures CO2 emissions from kiln operations and other cement production processes to prevent their release into the atmosphere.
Aluminum Industry
Key Emissions Sources:
- Energy-related Emissions: From fossil-based electricity consumption during smelting and thermal energy consumption during refining.
- Process Emissions: From the use of carbon-based anodes during smelting.
Key Solutions:
- Inert Anodes: Developed for use in smelting processes to reduce process emissions by eliminating CO2 production associated with traditional carbon anodes.
- Hydrogen Furnaces: Uses clean hydrogen as a reducing agent and energy source, reducing reliance on carbon-intensive fuels like coal.
Ammonia Industry
Key Emissions Sources:
- Energy-related Emissions: From fossil fuels used in traditional ammonia production processes.
Key Solutions:
- Blue Hydrogen Production: Involves generating hydrogen from natural gas through steam methane reforming (SMR) or autothermal reforming (ATR), while capturing and storing the carbon dioxide emissions using carbon capture, utilization, and storage technologies.
Industrial decarbonization is critical for mitigating climate change and achieving global climate goals. Tailored solutions across key sectors can significantly reduce emissions, fostering a sustainable future.
Ostara in the News
- Ahead of the Union Budget 2024, we spoke to CNBC-Awaaz and shared our views on the expectations of the Indian startup ecosystem from the budget. See the full video released on July 20, 2024 here.
Follow Ostara Advisors to stay updated with the latest trends related to Electric Vehicles, Innovation and Sustainability from India and around the globe.
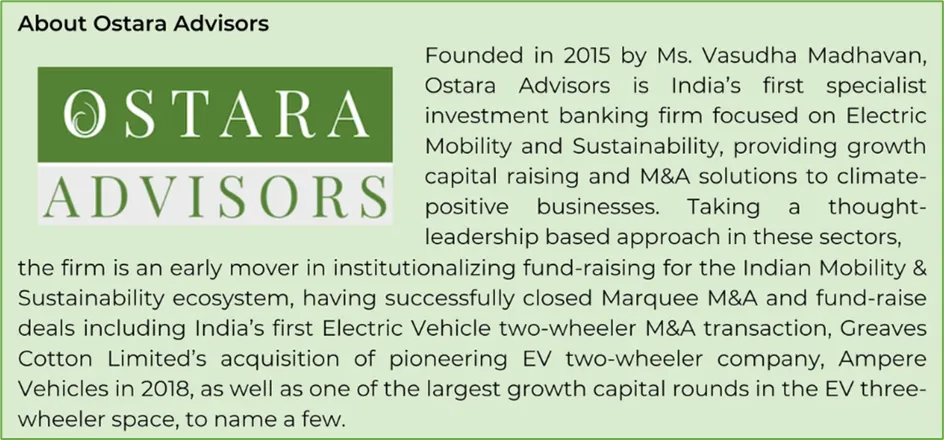